POPAI Awards Silver Sponsor 3A Composites Interview
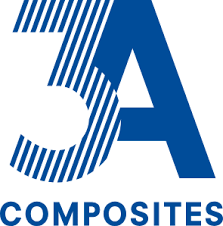
Take us through the market leading brands that 3A Composites manufactures…
We have 22 brands across the range, all of which are manufactured in our factories across Europe. DIBOND®, DILITE®, HYLITE®, FOREX®, FOAMALITE®, LUMEX®, DISPA®, KAPA®, SMART-X®, FOAM-X®, PERSPEX®, CRYLUX®, CRYLON®, AKRYLON®, PERSPEX® XT, HIPEX®, IMPEX®, IMPEX® MULTIWALL, POLYCASA® HIPS, POLYCASA® PS, POLYCASA® SAN and most recently SWEDBOARD®.
Anything new from 3A Composites that we should be aware of?
As a company we are always looking for ways to bring products to the market that will offer solutions to the customer. Last month we launched extruded acrylic sheets made from recycled PMMA. CRYLON®re, AKRYLON®re and PERSPEX® XT re comprising at least 95% recycled material from PMMA sheet waste, with no detriment to the quality and finish.
On top of that the exhibition market has been signalling for some time for a fibre based board with a Euroclass B level. We are able to offer that with our latest addition, SWEDBOARD® Fibre FR, a paper-based rigid board that is certified according to EN 13501-1: B-s1, d0. So it is a great sustainable option where a higher fire rating is required like airports, stadiums, exhibition centres and so on.
What else is the market telling you is a must-need from 3A Composites?
The three main aspects that arise are that; the products need to be more sustainable, easier to recycle whilst also not compromising on the quality and performance of the material. As a manufacturer throughout Europe we are able to minimise the distance our materials travel as they are locally produced. We are noticing a real interest from the market about origin of products and this is something we take seriously. We have always been transparent about the manufacturing process and around sustainability, we developed a classification system (FIVE-DOT-MISSION) which focusses on the use of materials, the CO2 content, the product life cycle and, of course, recycling, a topic of particular relevance for our products.
How do you explain to the market the differences between the large range of products you manufacture?
First of all, we get to know what it is that the customer requires, so that we are able to offer materials to suit their needs and give them guidance. In addition, as part of our corporate MISSION: TOGETHER. RESPONSIBLE., we have incorporated our products in the mission objectives and have created a system to classify them – the FIVE-DOT-MISSION. The five different categories in the system indicate the factors with the greatest impact on sustainability.
The FIVE-DOT-MISSION makes an assessment of each product on the basis of five categories and awards points per category.
The five categories are:
1. Biobased content
2. Recycled content
3. Co2 content
4. Product Lifecycle
5. Recyclability
As many as 3 points can be achieved in each of the categories, totalling a maximum of 15 points. According to the total number of points achieved (1-15), the FIVE-DOT classification is conducted using a defined colour gradation.
Our intention is to offer our partners guidance with their purchasing decision-making and to provide a transparent system.
That must make you the ‘One stop shop’ for everyone involved in POS/POP?
We are the largest substrate manufacturer in the world that offer such a vast and varied range of materials. So it is entirely our mission to find a solution from our portfolio of products, based off consumer needs and what values are important to them.
To do this, we work closely across the market from supply chain with our distribution partners, fabricators working with the material, to the brands and retailers looking to achieve a concept and vision.
In order to find the right solution we work closely with all players in the process to understand the situation and are on hand to offer technical advice, support and work tirelessly to enable these projects come to completion.
Find out more from 3A Composites HERE