Vacuum forming is a commonly used process for producing hollow 3D parts such as trays. A sheet of plastic is heated and then drawn over a shaped tool using a vacuum. Tooling can be made cheaply for small runs using wooden tools. Metal tools can be produced for larger runs. Vacuum formed parts generally need to be released after moulding in one direction, which limits the complexity of the parts. They also need to have large draft angles, as the part contracts onto the tool as it cools. When the plastic is drawn onto the tool, the sheet wall thickness is thinnest where the tool is the highest. As a result, the process works best for shallow parts.
Parts generally need to be finished after forming, with edges cut off using simple guillotining or more complex 3D routing. There is an element of waste involved in this process. If printing onto the formed parts is required, it's generally easiest to preprint the plastic sheets, making an allowance for the 3D distortion of the graphic.
Below is a list of plastics materials suitable for use in vacuum forming production methods.
|
|
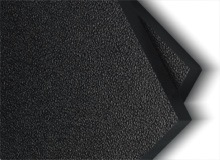
|
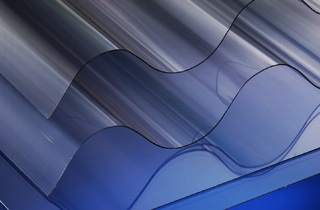
|
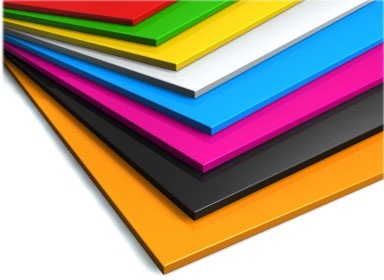
Discover the benefits & limitations of HIPS Click here>
|
|
|
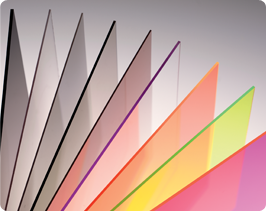
|
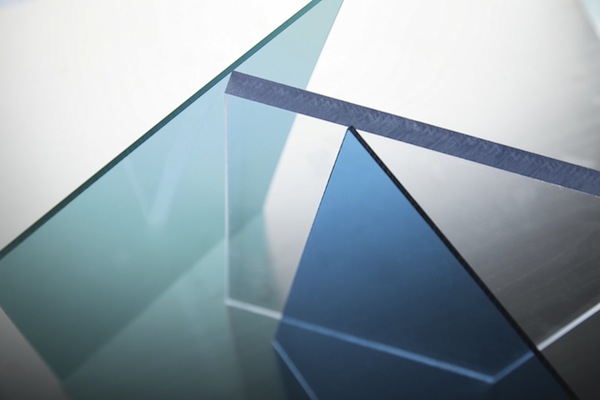
|
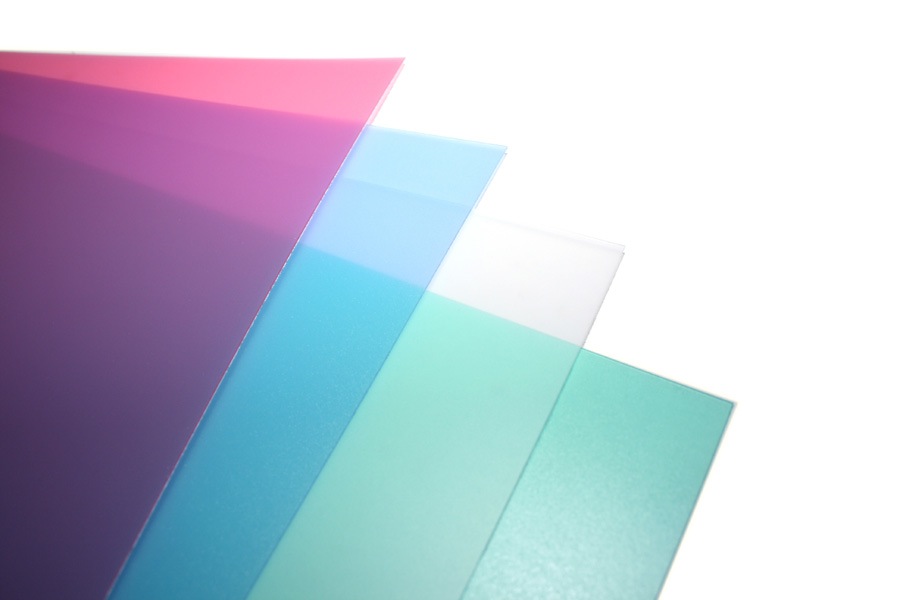
|
|
|

Explore the material properties, benefits & limitations of Rigid PVC Click here>
|
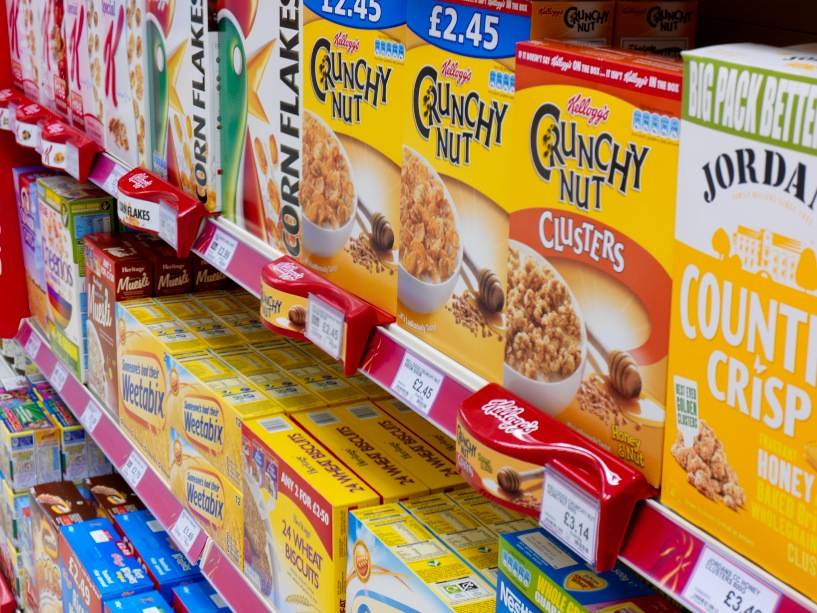
View our gallery of P-O-P displays created with plastics Click here>
|
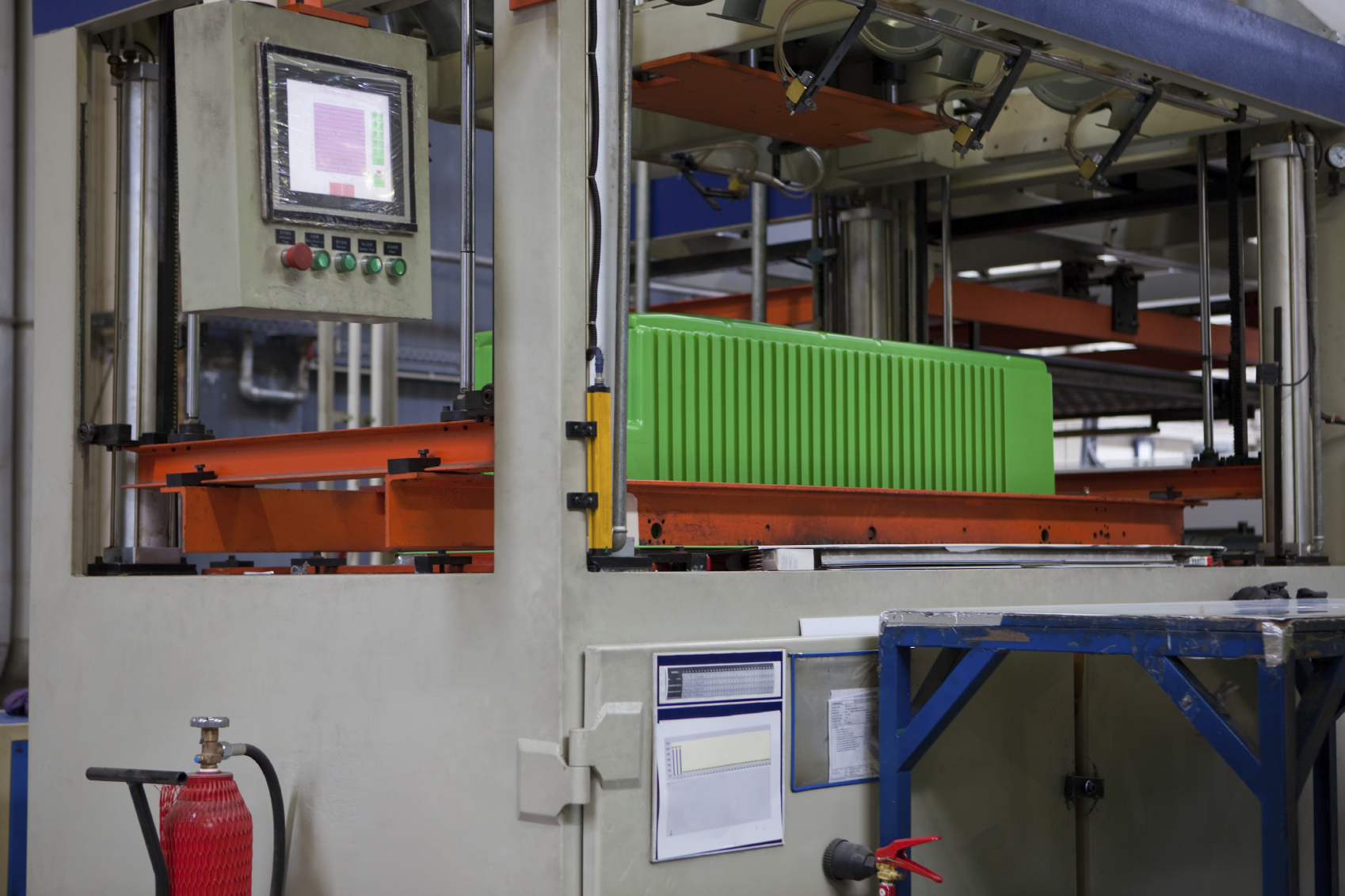
See a short video of Vacuum Forming in action. Click here>
|